Soldadura MIG pulsada
- Máquinas Bustamante
- 24 nov 2022
- 4 Min. de lectura
Algunas de las fuentes de energía de última tecnología en el mercado actual son aquellas que brindan capacidades pulsantes. Lo más probable es que hayas escuchado cómo estas sofisticadas máquinas facilitan la soldadura para el operador y brindan una soldadura de alta calidad. Pero, ¿sabías que estas máquinas realmente proporcionan un ahorro de costos? Aunque inicialmente podés pagar un poco más por estas fuentes de energía, las ventajas que brindan reducirán los costos generales de soldadura y compensarán tu inversión a largo plazo.
Las ventajas que ofrecen las máquinas de pulsos incluyen:
Ahorro de cables y gas
Las máquinas MIG pulsado ofrecen un rango de operación más amplio porque extienden el rango bajo y alto de cada diámetro de alambre. Por ejemplo, antes de que el operador tenga que almacenar .035 ”, .045” y .052 ”diámetros de alambre para diversas aplicaciones, pero con MIG pulsado, .045” puede extenderse en el rango inferior y superior para que pueda ser utilizado para una variedad de aplicaciones. Lo que esto significa es que en lugar de tener dos o tres cables de diferentes tamaños, un operador solo necesitaría uno. Tener un tipo de cable minimiza los costos de inventario y reduce los tiempos de cambio. Lo mismo ocurre con el gas protector: un gas puede alcanzar tanto el rango bajo como el alto de la aplicación. Además, los diferentes tipos de repuestos (pistola, puntas de pistola, revestimientos, etc.) se reducen para ahorrar costos adicionales.
Reducción de salpicaduras y humos
Comparado con el MIG convencional, Pulsing ofrece menos salpicaduras y humos. La reducción de las salpicaduras se traduce en importantes ahorros de costos porque se aplica una mayor parte del alambre fundido a la unión soldada, no como salpicaduras de superficie sobre el producto y los accesorios circundantes. Esto también significa menos tiempo de limpieza. La reducción de los humos de soldadura crea un entorno más seguro y saludable para toda la planta o el taller.
Reducción de calor
La pulsación ofrece una entrada de calor controlada que conduce a una menor distorsión y una mejor calidad y apariencia general, lo que significa menos problemas de producción. Esto es especialmente importante con el acero inoxidable, el níquel y otras aleaciones que son sensibles a la entrada de calor.
Productividad mejorada
MIG pulsado ofrece altas tasas de deposición. Además, dado que las nuevas máquinas son más simples y adaptables, es más fácil soldar con MIG pulsado que con otros métodos de transferencia, y se dedica menos tiempo a la capacitación.
Mejor calidad
Todas estas ventajas de MIG pulsado descritas anteriormente dan como resultado una mejor calidad general del acabado y un arco más estable. Además, los operadores están recibiendo un entorno de trabajo de mejor calidad, ya que no tienen que lidiar con humos, salpicaduras ni tiempo extra de limpieza o molienda. Un beneficio más es que las fuentes de energía sinérgicas permiten que estas soldaduras de alta calidad sean logradas por aquellos con relativamente menos entrenamiento.
¿Qué es MIG pulsado?
En términos simples, MIG pulsado es un método de transferencia sin contacto entre el electrodo y el charco de soldadura. Esto significa que en ningún momento el electrodo toca el charco. Esto se logra mediante la manipulación a alta velocidad de la salida eléctrica de la máquina de soldar. Está diseñado para ser un proceso sin salpicaduras que se ejecutará con una entrada de calor más baja que los métodos de transferencia globular o por aspersión.
El proceso MIG pulsado funciona formando una gota de metal fundido al final del electrodo por pulso. Luego, se agrega la cantidad justa de corriente para empujar esa gota a través del arco y hacia el charco. La transferencia de estas gotas se produce a través del arco, una gota por pulso.
Para comprender este proceso en detalle, echemos un vistazo a una forma de onda. A diferencia de CV (voltaje constante) donde la corriente está representada por una línea recta, el MIG pulsado reduce la corriente en momentos en que no se necesita energía adicional, enfriando así el proceso. Es este período de "enfriamiento" el que permite que el MIG pulsado suelde mejor en materiales delgados, controle la distorsión y funcione a velocidades de alimentación de alambre más bajas.
Durante el proceso, la corriente se eleva a un pico cuando se forma la gota. Luego, en la fase de corriente de fondo, la corriente se reduce para reducir la entrada de calor general. Es la altura y el ancho del pico lo que es importante para una transferencia adecuada.
MIG pulsado en comparación con otros métodos de transferencia
¿Cómo se compara el MIG pulsado con otros modos de transferencia de soldadura? Examinaremos cada uno con sus ventajas y desventajas.
Cortocircuito
En cortocircuito, el cable toca la pieza de trabajo y se corta a sí mismo. Esta es la forma más fría de soldadura que todavía ofrece una buena fusión. El cortocircuito permite a los operadores soldar tanto material grueso como fino en todas las posiciones. También tiene el beneficio de un charco pequeño que se solidifica rápidamente. Sus desventajas incluyen velocidad de alimentación de alambre limitada y tasas de deposición. También existe el peligro de "lapeado en frío" en metales más gruesos. Aquí es donde no hay suficiente energía en el charco para fusionarse correctamente. El cortocircuito también produce una mayor cantidad de salpicaduras en comparación con los otros métodos de transferencia.
Globular
El modo de transferencia globular es básicamente un cortocircuito incontrolado. Se caracteriza por un gran volumen de metal de soldadura que sale del electrodo. Estas gotas grandes se pellizcan en el arco y caen en el charco. Este método de transferencia produce una gran cantidad de salpicaduras, así como un alto aporte de calor. Además, globular se limita a soldaduras de filete planas y horizontales. A menudo es común una menor fusión porque la salpicadura interrumpe el charco de soldadura. Además, debido a que la transferencia globular utiliza más cable, generalmente se considera menos eficiente.
En el lado positivo, la transferencia globular se ejecuta a altas velocidades de alimentación de alambre y amperajes para una buena penetración en metales gruesos. Además, se puede utilizar con gas protector de CO2 económico. Se utiliza principalmente cuando la apariencia no es un problema.
Arco de pulverización
El arco de pulverización impulsa una pequeña gota fundida del electrodo al trabajo. Es un proceso CV puro que debe producir suficiente corriente para enviar una corriente constante de metal fuera del electrodo. Sus ventajas incluyen altas tasas de deposición, buena penetración, fuerte fusión, buena apariencia de soldadura con pocas salpicaduras.
Sus desventajas incluyen un alto aporte de calor, un rango limitado de posiciones de soldadura y la propensión a quemarse en materiales delgados.
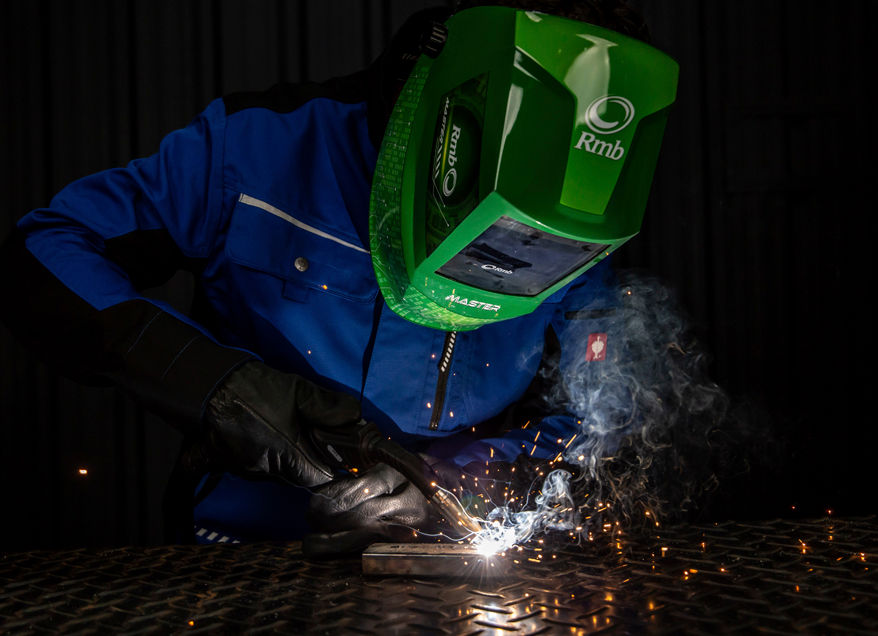
Comentarios